EDUCATION
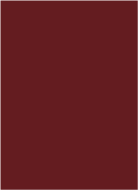
Cork Oak Forests
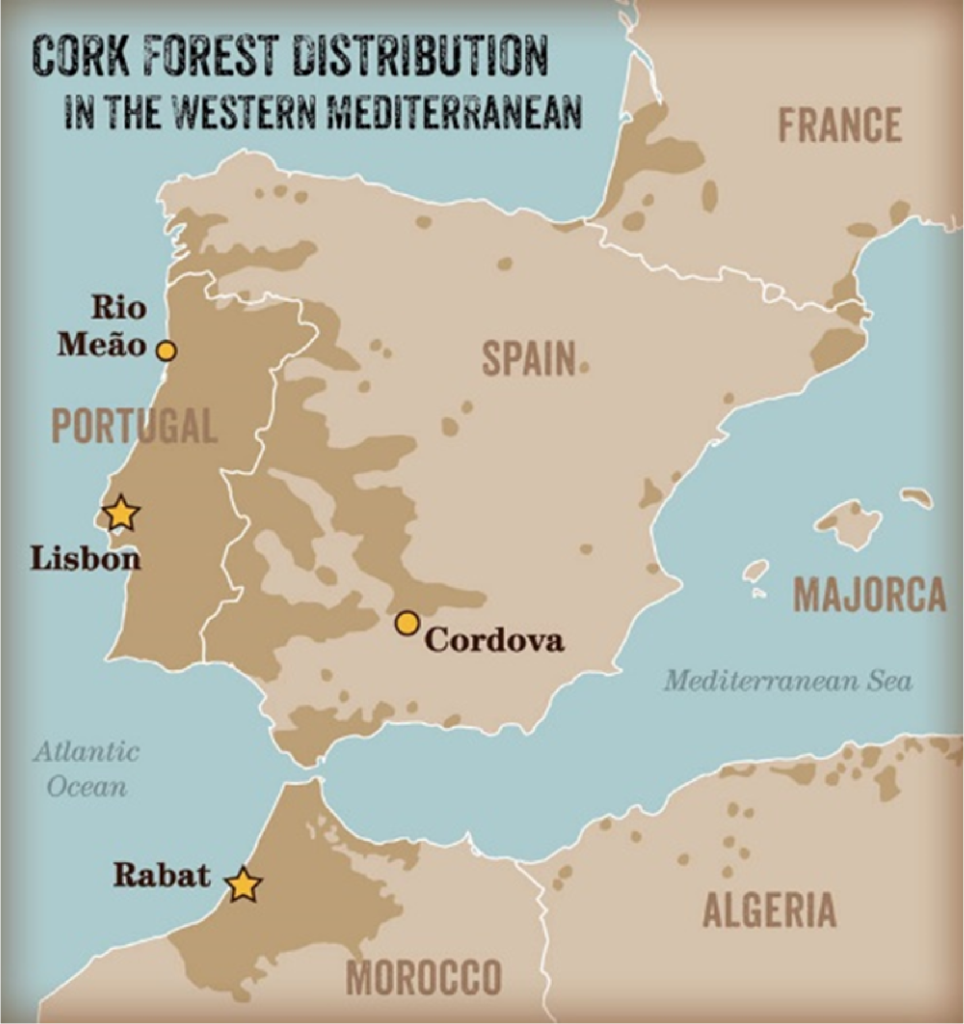
Cork is a tremendous material, and in our humble opinion, it is one of the most amazing materials to exist, naturally, in nature. ‘Cork’ as it is known, is the outer layer of the cork oak tree, Quercus Suber L. The cork oak tree is native to the Western Mediterranean Basin, where it finds these ideal growing conditions:
- Sandy, chalk-free soils, with low nitrogen and phosphorus, high
potassium levels and ph of 4.8 to 7.0 - Rainfall 400-800 mm (16–32ins) a year
- Temperature between -5o C and 40o C
- Altitude 100–300 meter (330–990 ft)
In total, there are over 2.2 million hectares of cork forests (called Montados in Portuguese), with an annual global production around 340,000 tons a year, which are spread across Portugal, Morocco, Spain, France, Italy, Algeria and Tunisia. In Portugal, where we source the majority of our material, they have 1/3 of all the cork forests in the world, with roughly 23% of their forested land being covered with cork forests, while this accounts for over half of global cork production. In Portugal, the cork supplies are expanding at roughly 10,000 hectares a year, largely in part to a reforestation program supported in part by the Portuguese Government and the European Union. With these programs in place, coupled with the socio-economic value cork provides Portugal, all signs indicate for a continual increase of available material over time – increasing the sustainability of a sustainable resource.
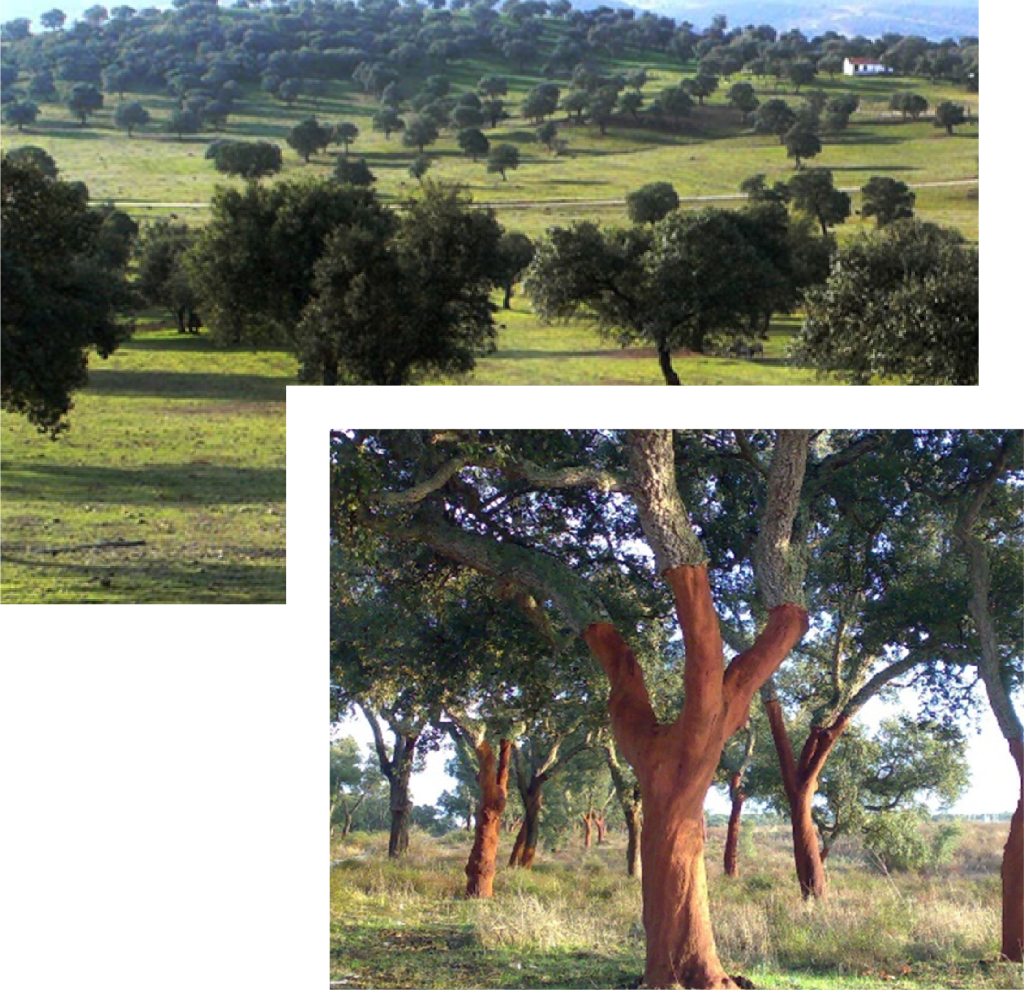
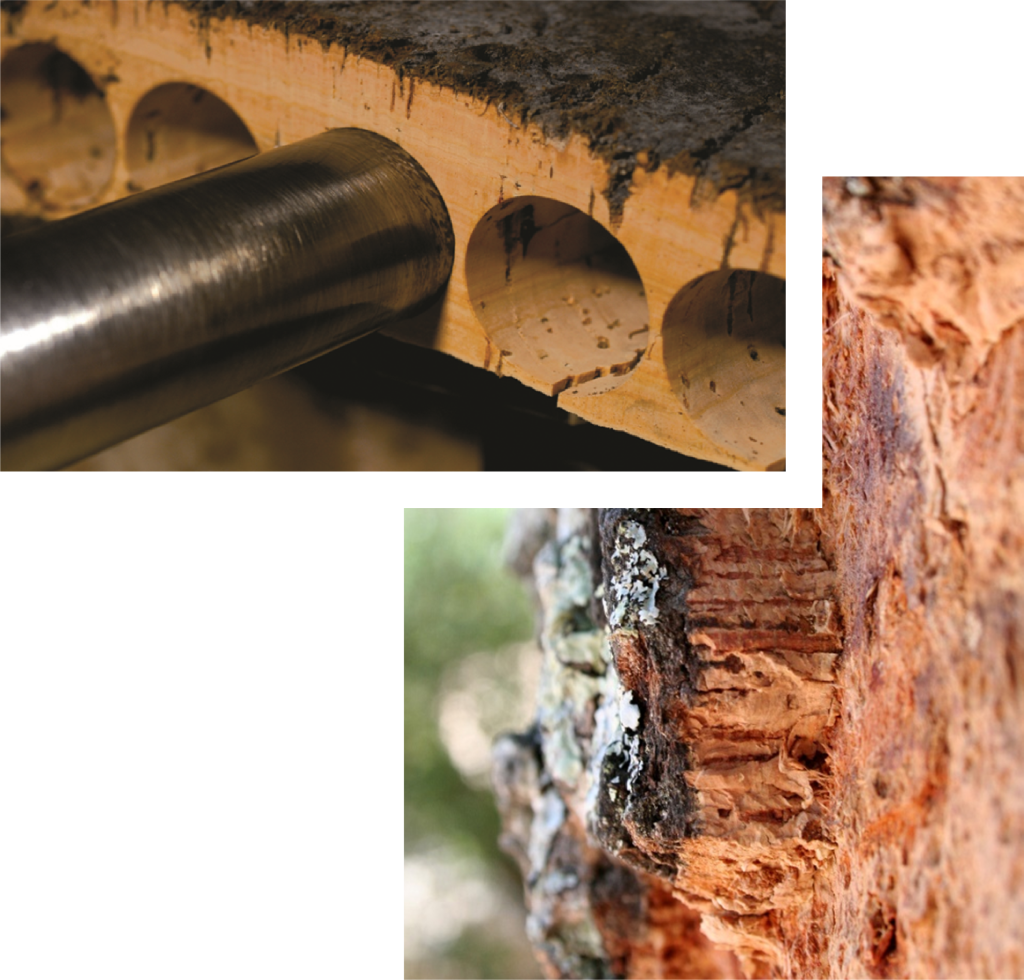
Cork forests not only contribute to a mixed agrarian economy that has sustained farmers for many centuries, but they also support a unique and fragile ecology that provides a habitat for endangered species. The cork oak helps protect the soil from desertification and is well suited to the hot, arid conditions of southern Portugal. It is far less susceptible to the wildfires that ravage eucalypt and pine forests in the north of the country from time to time.
Cork is a multi-functional and multi-purpose material. Besides its ecological value, every part of the tree serves some useful economic purpose. More than 50% of the cork bark goes into the production of different types of stoppers/enclosures for the bottling industry, while other products leverage corks tremendous inherent technical properties relating to sound absorption, thermal insulation, vibrational dampening, lightness and ultimate resilience, in their use in ‘value-ad’ manufacturing and product development.
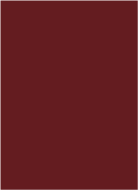
Cellular Structure
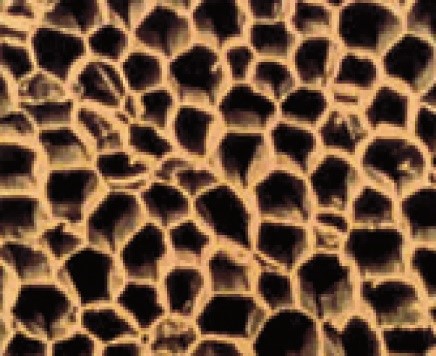
(Honeycomb Cork Cell Structure)
The ecological value of cork as a raw material goes without saying, especially when you consider its renewable characteristics, but when it comes to analyzing its’ functional value, you don’t need to look much beyond its cellular structure to get a high-level overview of why it is such an impressive material. Cork’s structure is very similar to that of a honeycomb, with each cubic centimeter containing around 40 million cells (or 200+ million per cubic inch). These cellular pockets are minute, straight-sided pentagonal or hexagonal prisms. The cell height rarely exceeds 0.045 mm, and with that said, the height decreases to between 0.01-0.02 mm in the last cork bark that is formed in the autumn. These cells are filled with a gaseous mixture (like air).
Chemically speaking, the composition of cork is:
- Suberin (approx 45%) is the main component of the cell walls; almost completely impermeable liquids and gases, it is also fire
and insect resistant and unaffected by water; responsible for the resilience of the cork. - Lignin (approx 20%) – the binding compound responsible for cork’s unique structure.
- Polysaccharides (approx 20%) cell components that help define cellular structure.
- Ceroids (approx 5%) – hydrophobic compounds that ensure water imperviousness.
- Tannins (approx 5%) – polyphenolic compounds.
- Remaining compounds (≤ 5%) are normally called extractable and are organic components of cork’s cell walls, although they
are not considered structural compounds of cork.
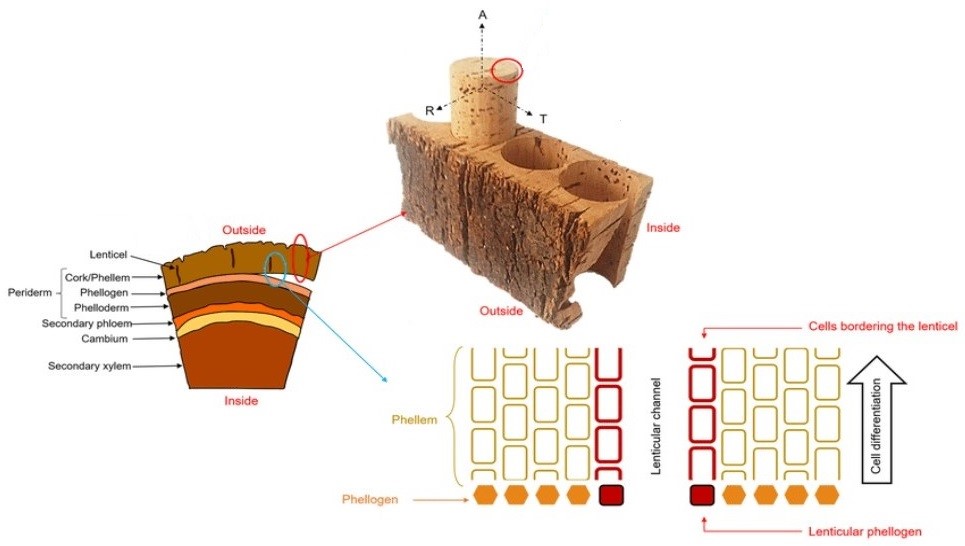
Representation of the transverse section of cork tree:
Connecting (red arrow) – showing cork stopper plug from bark (letters A, R
and T refers to as the axial, radial and tangential directions, respectively).
Connecting (blue arrow) – showing enlarged section of the phellogen
region with cellular differentiation.
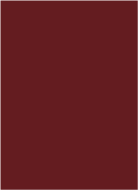
Functional Value
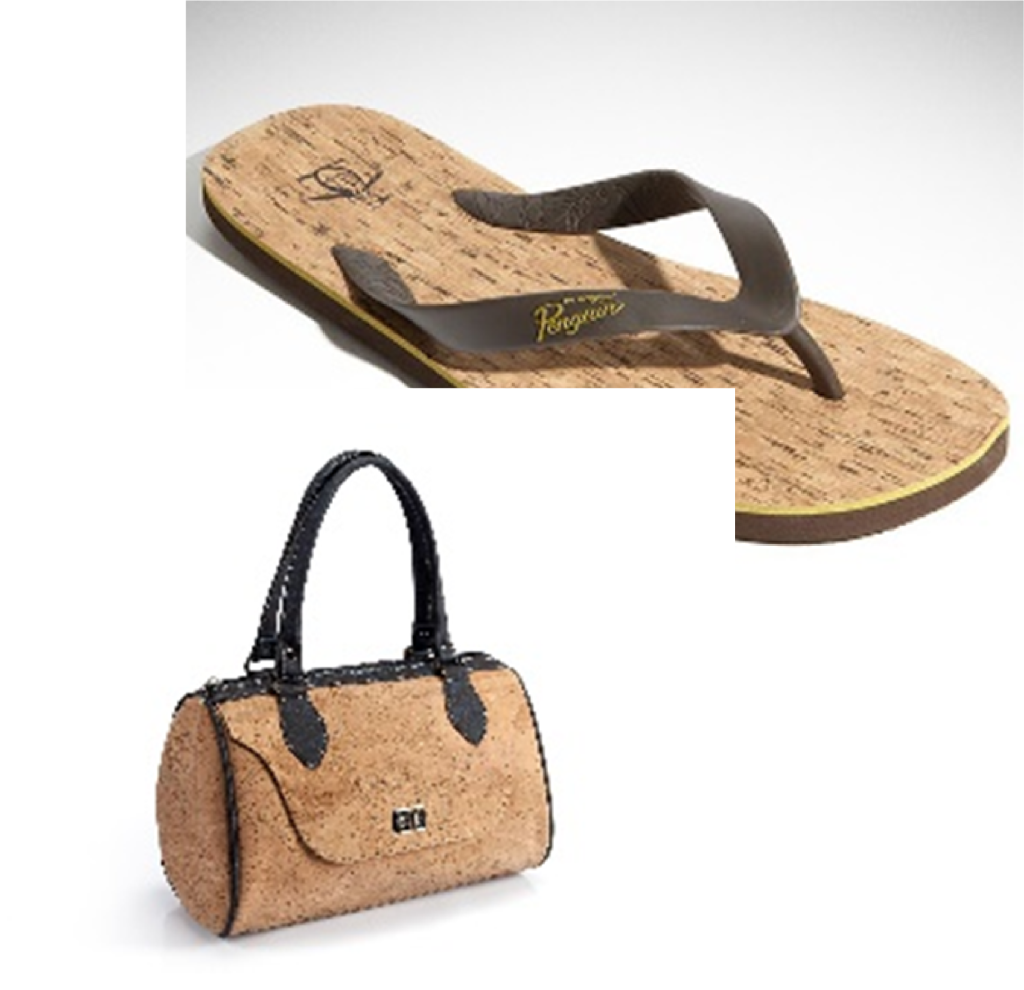
(Footwear & Vegan Cork Leather Purse)
The fact that cork is essentially made up of thousands and millions of cellular pockets of air is the key to what makes cork so remarkable. Air is an insulator when trapped, and not only provides thermal value (meaning that it is both “warm to the touch” and can be used for thermal insulation and isolation), but it also inhibits the passage of sound and/or vibrations – all naturally (without additives).
In addition, cork has tremendous rebound and flexibility under compression, creating a quality of ‘give’. Cork can be compressed to about half its width without losing flexibility. It is the only solid that can be compressed in one dimension without increasing in another dimension, showing a high degree of dimensional stability. Cork also has tremendous elastic memory, which provides ‘rebound’, and is the response to the compression when it occurs. When compressed, and the point of compression is removed, the cells will return to their original size. Though relevant when used for flooring, as it provides fraction that enables traction, this characteristic is most easily recognized in bottling applications, as a cork is compressed to be put in a bottle, and while there it maintains a tight and integral seal (regardless of the temperature and pressure variations introduced). Once it is removed, it expands again, and can only be re-inserted by compressing the cork into the neck of the bottle.
Cork is extremely light, weighing only 0.16 grams per cubic centimeter (as most of its volume consists of air-like gas). It resists moisture and can age for long periods without deteriorating. Cork is permeable, yet impermeable at the same time – presenting an interesting dichotomy. Cork is waterproof but can absorb moisture in the top microscopic cell layer, helping retain moisture, without letting it pass through. Proof of this concept need not look beyond personal experience and realizing that when you uncork some red wines, you find a red stain on bottom surface of the removed cork, but it doesn’t permeate through the cork. Being that cork is impermeable beyond the cellular level, it excels in water prone applications, though care should be taken depending on what the cork may be adhered to, or if it is made with glue. But, as a mass, the cork bark is impermeable, so it can be used in wet applications, and the water will not affect it.
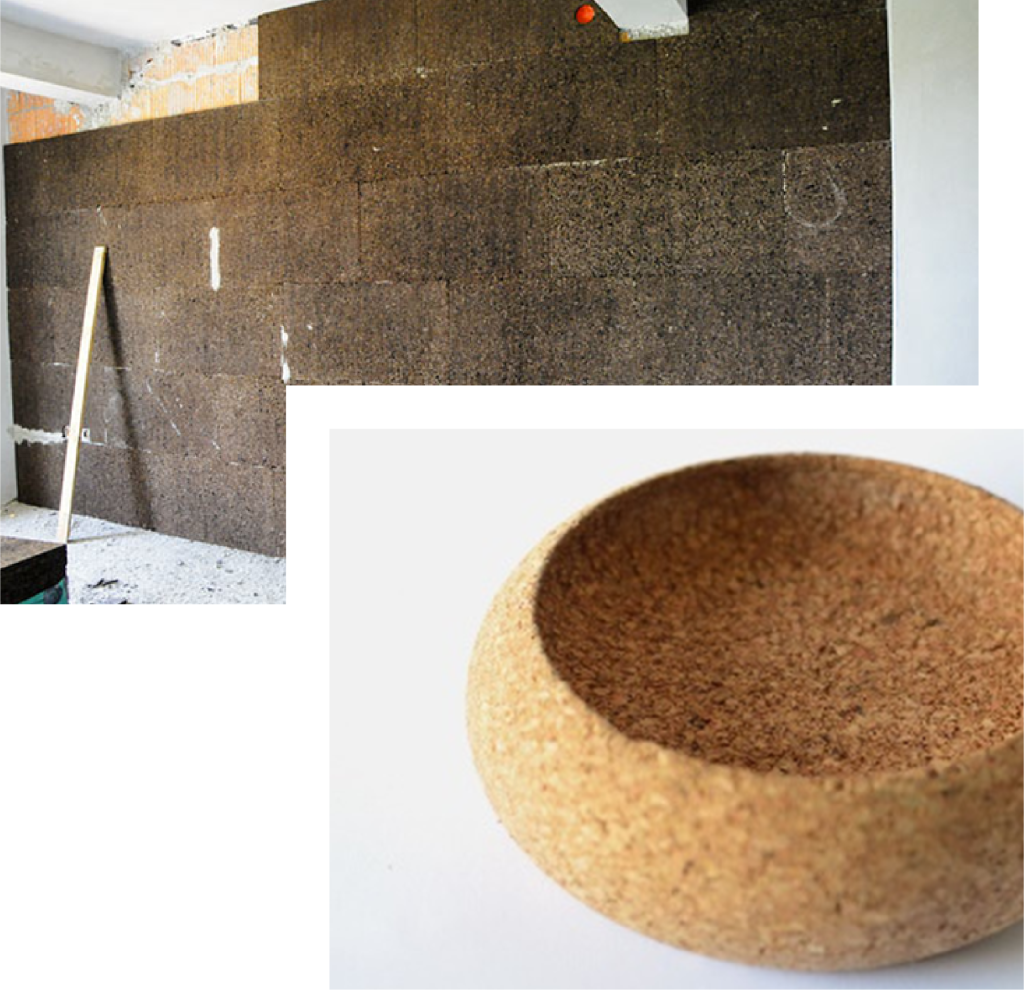
(Wall Insulation & Decorative Bowl)
The degree of value and range of importance of these attributes obviously varies based on the intended use and purpose, but what is clear is that cork as a ‘natural’ raw material provides benefits that the most re-engineered, and often chemically laden materials, often cannot re-create. Score one for nature!
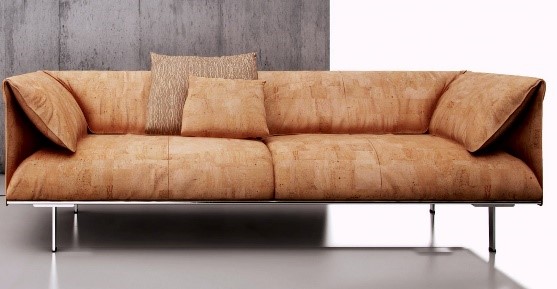
(Furniture)
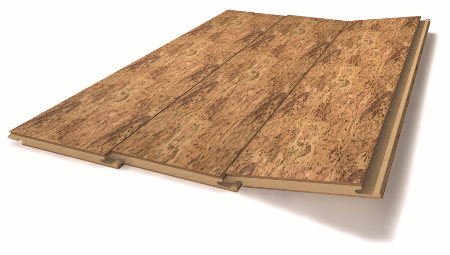
(Flooring Plank)
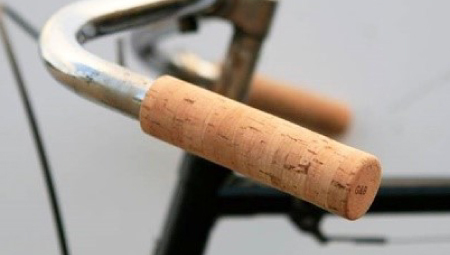
(Flooring Plank)
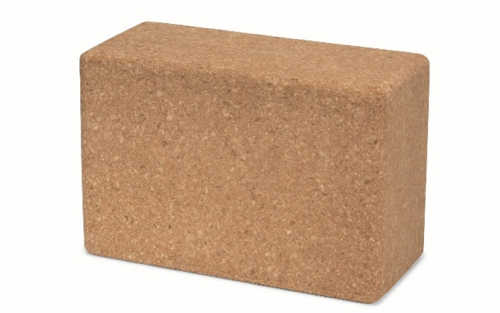
(Yoga Block)
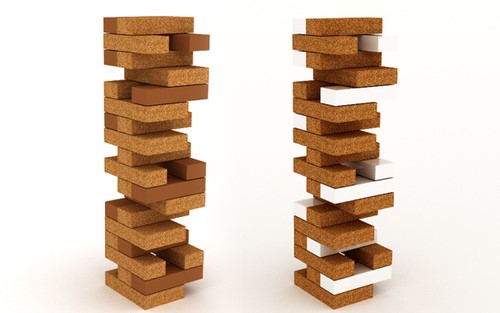
(Toy Blocks)
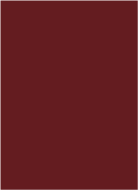
Ecological Value
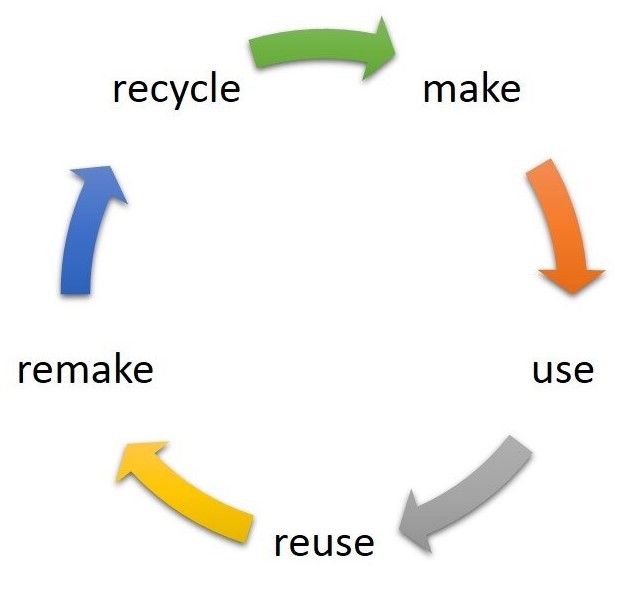
(Closed loop system = circular economy)
Cork is natural, biodegradable, renewable and recyclable. Each part of the cork tree serves an ecological or economic purpose, and through efficient production, it is a closed cycle system where everything is used, and there is no waste. Relative to actual wine corks, there is almost no energy used in their production, as compared to any synthetic plastic or screw-top alternatives which have been introduced over the last several decades.
The cork oak forests play an important role in helping suppress climate change. The cork oak tree is a sequester of carbon, meaning that it absorbs carbon dioxide from the atmosphere and stores it in its wood and bark of the tree. As the bark is harvested and used in products, that sequestered carbon locked into the product, storing it. A cork tree, which has its bark removed every 9 years, will absorb 3-5 times as much CO2 as would a similar tree that did not have its’ bark removed so it could regenerate. According to the leading cork supplier in Portugal, cork oak forest can sequester up to 73 tons of CO2 from the atmosphere for each ton of cork produced.
The cork forests of the Mediterranean support one of the world’s highest levels of forest biodiversity, second only to the Amazon Rainforest. There are more than 160 bird species, 37 species of mammals, and 24 species of reptiles and amphibians. The birds find protection in the forests, so they can nest and feed their young. Mammals, including wild boars and Iberian lynxes, can thrive in the cork forests. The Iberian Lynx, the most iconic of the Portuguese mammals
was teetering on extinction until recently. In 2002, there were less than 100 Iberian lynx left in the wild, but due to conservation efforts by the governments of Portugal and Spain, these numbers are rebounding, and as of a 2022 report, there were over 1,000 wild Iberian lynx throughout Portugal and Spain.
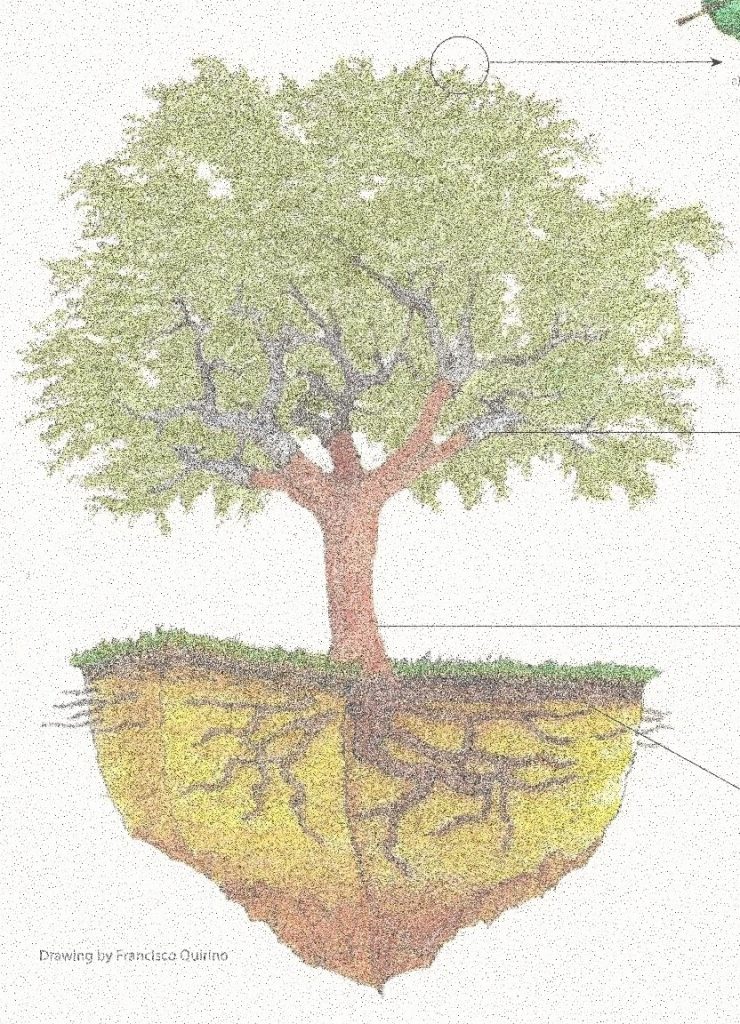
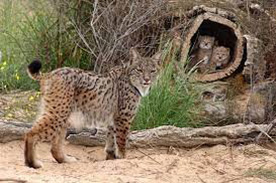
(Iberian Lynx)
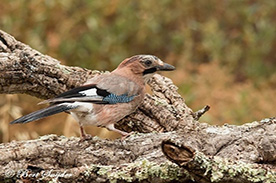
(Iberian Lynx)
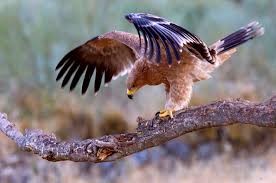
(Spanish Imperial Eagle)
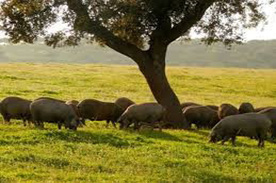
(Wild Boar)
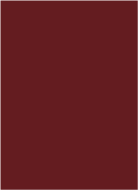
Historical Uses
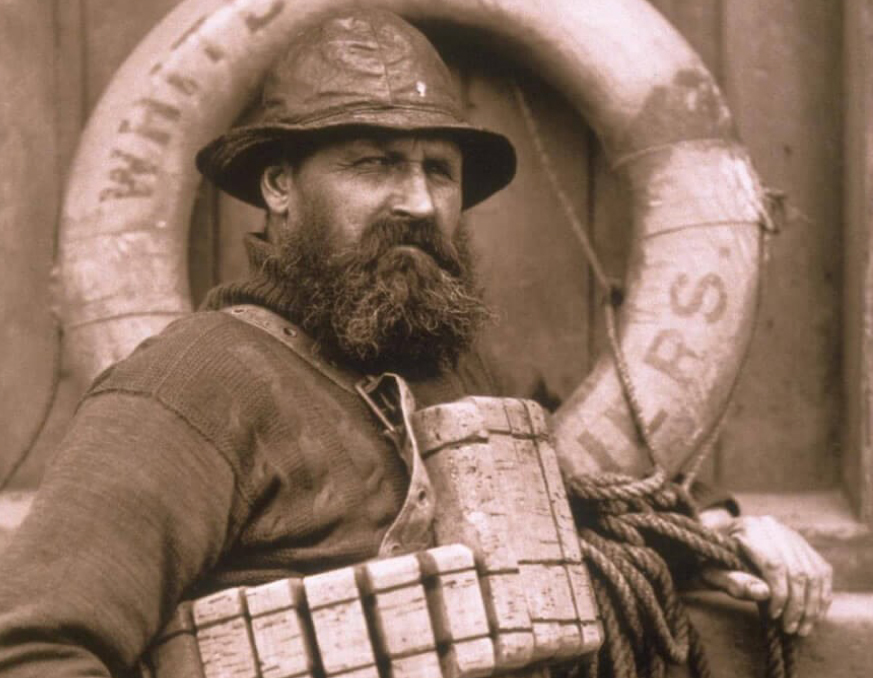
Cork has been used by humans dating back to 3000 BC. Originally used in China, Egypt, Babylon, and Persia as fishing tackle and buoys, it wasn’t until the 4th century BC that the first use of it being used for wine bottling was documented. In the early 1200’s, Portugal adopted a pioneering position with environmental legislation geared at protecting their cork forests once they began to realize it’s true value and importance. Portuguese shipbuilders in the 14th century used cork trees to make the masts for their vessels as it had been shown to be exceptionally strong and wouldn’t rot – putting them on good standing as they set out to explore distant lands during the Age of Discovery.
It wasn’t until the 18th century when an English Physician was first able to analyze cork under the microscope and was able to really determine how and why cork was such an important material. It was then discovered that the outer layer of bark (the periderm) contained an extremely high level of suberin, which is a rubbery substance that acts as a natural moisture barrier for plants. Millions of microscopic air chambers are formed from suberin as the bark grows, which allows the cork to float as well as repel moisture from penetrating into the material. You may also note the scientific name for the cork oak tree, Quercus suber, is the derivation of the word suberin. Also in the 18th century, Dom Pierre Pérignon, the monk and treasurer of the Hautvillers Abbey, began to use cork to seal bottles of his famous Dom Pérignon champagne (the brand still in existence, and still using cork to this day).
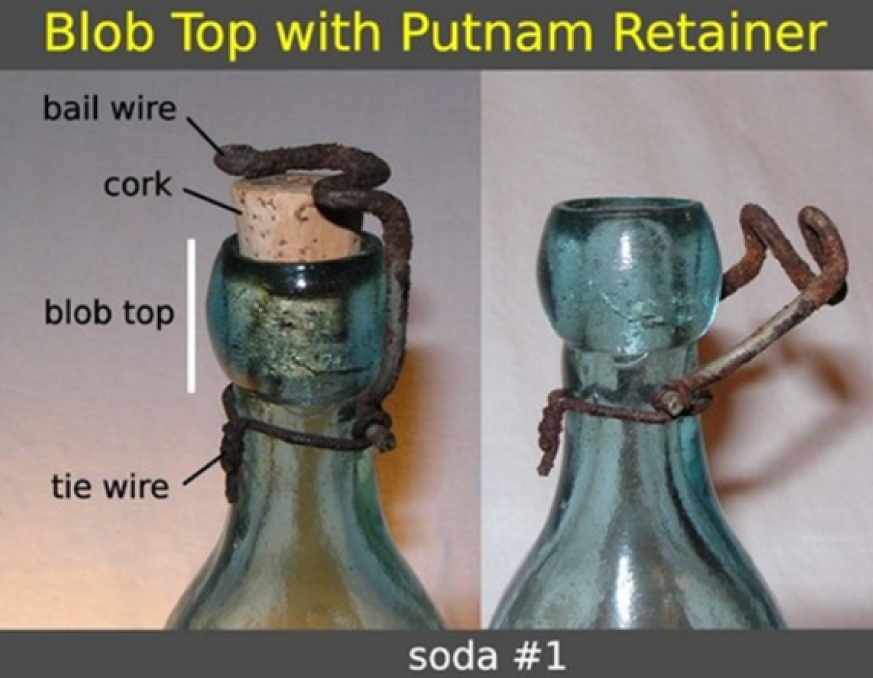
It appears that the cultivation of cork, at least in a systemic/forest approach, didn’t really start in Portugal until the late 1700’s, when the use of cork stoppers became more common. Then in 1790, an Italian chemist analyzed cork’ chemical composition, spurring its industrial relevance even more. The 19th century was really when ‘work’ around cork started to occur throughout the world, starting the United Kingdom with the first patent for making cork stoppers. Then in the early 1900’s, a patent for binding cork granules with adhesive was created. In WWII, cork was used in vehicle transmission belts, and as a component in tires.
In the 1950’s, though flooring had been around for many decades already, its’ use with a pre-applied topical coating was developed. Cork has been used in shoes (most famously in Birkenstocks), in the development of a natural leather alternative, is used as a thermal retardant in certain building products, has been used by NASA on spaceships, and really the innovations keep coming. Cork as a material is ripe for development, especially as its’ value is becoming more understood and accepted, and the importance of sustainability has become mainstream.
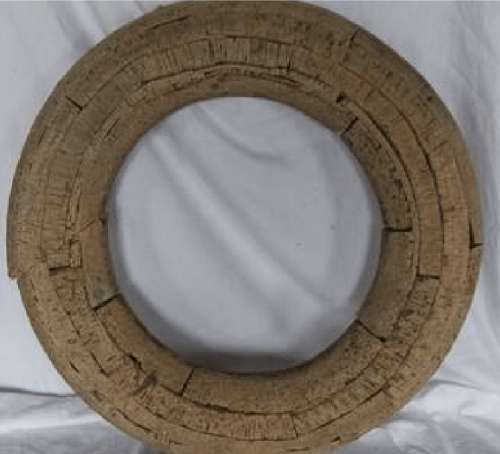
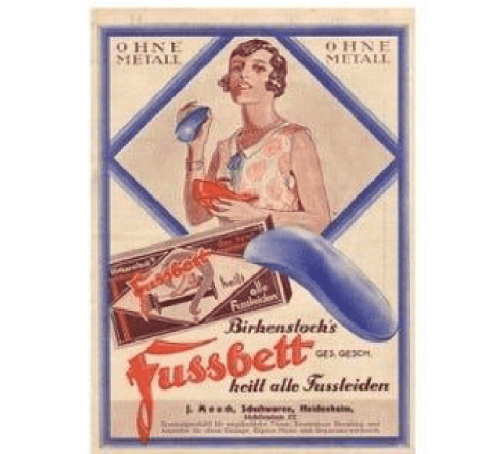
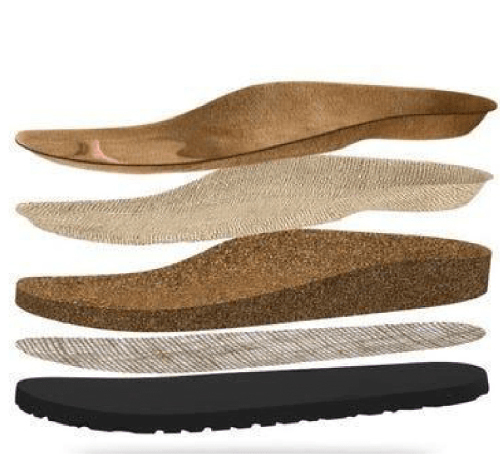
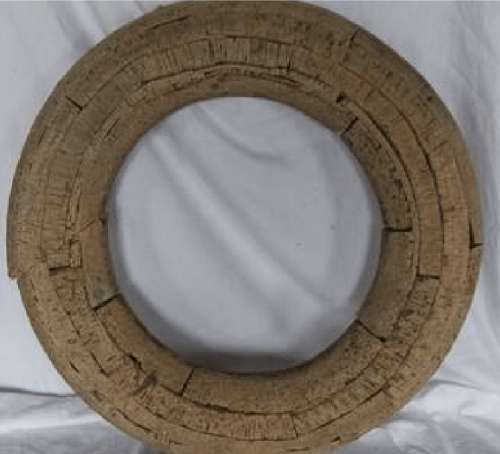
(Cork Life buoy (late 1890’s))
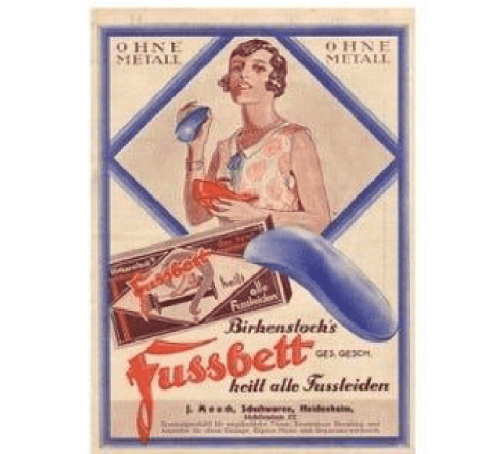
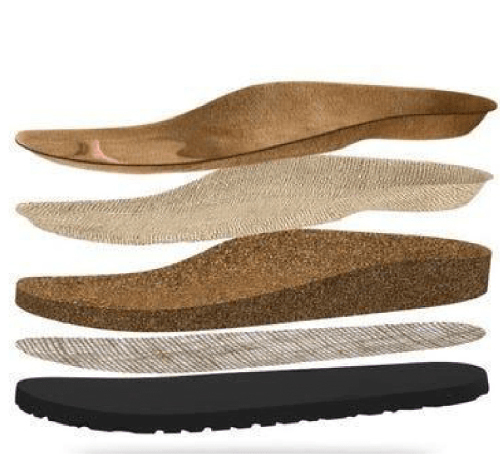
(Early Birkenstock advertisement)
(Cork Life buoy (late 1890’s))
(Early Birkenstock advertisement)
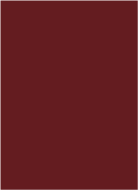
Granulating
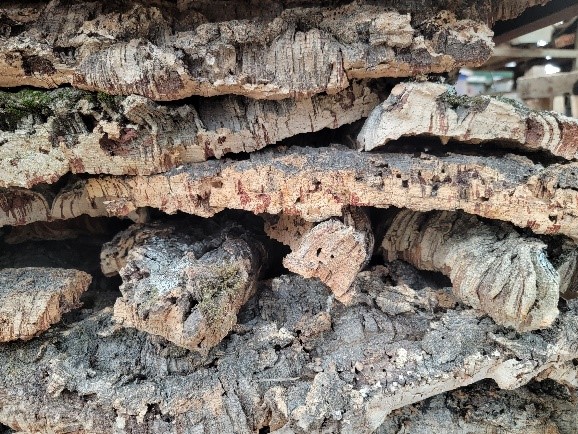
(Cork Bark chunk)
The granulation of cork is a process that involves grinding larger chunks of the cork into smaller granules, with the granule size being driven by the materials’ intended use.
But before it makes sense to delve into the topic of granulation, it is prudent to provide an overview of the different types of cork, and when and where it comes from. The ideal, and high value cork is the stuff that comes off the mature trees on the 9-year harvesting cycle. The primary use is in stopper production, but slabs for veneering and other applications are also provided value-add to the material. The waste from all this production (ie: that left from wine cork making, slab cutting, etc.) tends to be quite clean, tan in color, and relatively pure.
There is another category of cork which is inferior in quality, with the determining factor of can it be used to produce wine corks – which is can’t. This material has several origin points, that include coming from ‘virgin’ cork (cork that comes from the first harvest of the tree – at year 25), that which comes from the branches that are pruned, and material taken from forest fire damaged trees. The nature of this material is that it all tends to have high resin content, which makes it ideal material to process via an autoclave method (though described in the ‘bonding’ section, simplistically autoclaving involves an intense steaming process that converts the suberin in the cork into an internal binding agent).
In total, there are over 2.2 million hectares of cork forests (called Montados in Portuguese), with an annual global production around 340,000 tons a year, which are spread across Portugal, Morocco, Spain, France, Italy, Algeria and Tunisia. In Portugal, where we source the majority of our material, they have 1/3 of all the cork forests in the world, with roughly 23% of their forested land being covered with cork forests, while this accounts for over half of global cork production. In Portugal, the cork supplies are expanding at roughly 10,000 hectares a year, largely in part to a reforestation program supported in part by the Portuguese Government and the European Union. With these programs in place, coupled with the socio-economic value cork provides Portugal, all signs indicate for a continual increase of available material over time – increasing the sustainability of a sustainable resource.
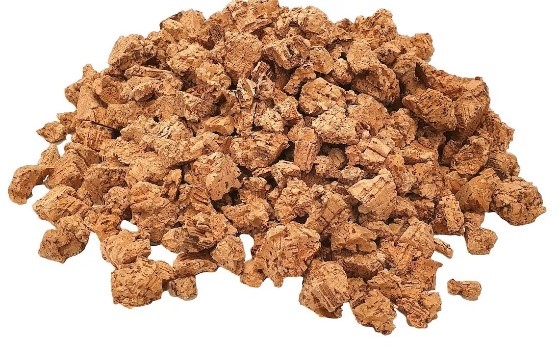
(Natural Cork Granules)
Due to its source and origin, and the way it is accumulated having a greater amount of wood and dirt contamination within it, the granules tend to be left in a larger size, and therefore used in different applications (and for different purposes based on how the cork internally changes in the autoclaving process). For acoustic applications the granules used tend to be in the 3-10mm range, while for thermal proposals, larger granules ranging for 5-22 mm are used.
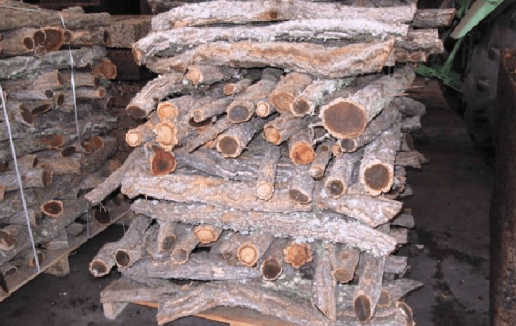
(Cork Branches)
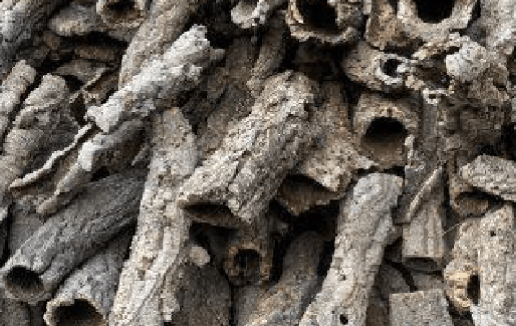
(Virgin Bark Tubes)
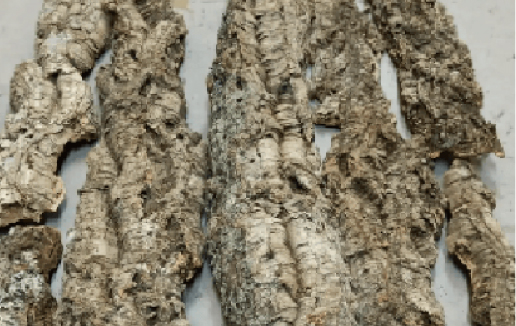
(Virgin bark chunk)
The granules are then cleaned to remove impurities using either densiometric or pneumatic separators or rotating drums, and
then sorted to size for their application.
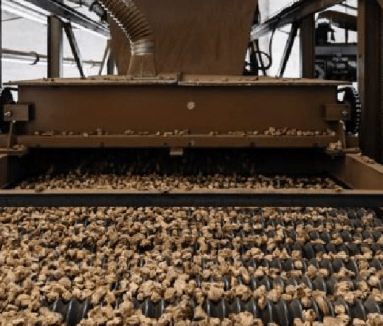
(Larger size granulation
and sorting )
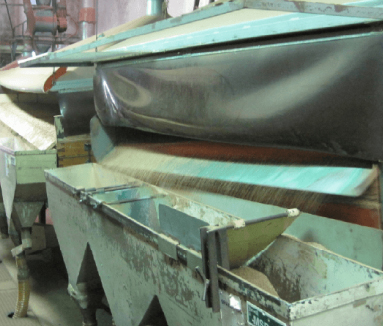
(Finer size sorting)
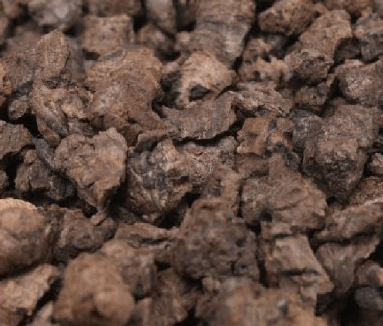
(Larger ‘autoclaved’ granules)
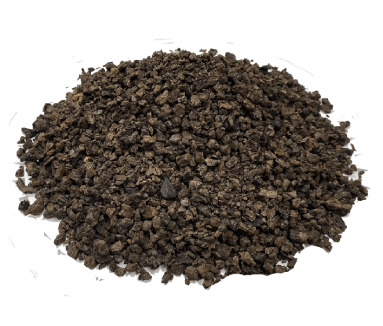
(Further granulated ‘black’
cork (from autoclaved process))
Depending on the application, the cork granules are sorted in ranges from less than 1mm, all the way up to 25mm in size. The majority of agglomerated options tend to range from the 1-5mm size.
(Common granulation sizes)
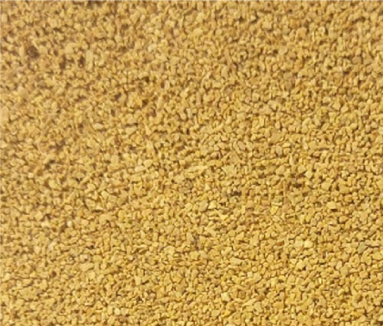
(0.5-1mm)
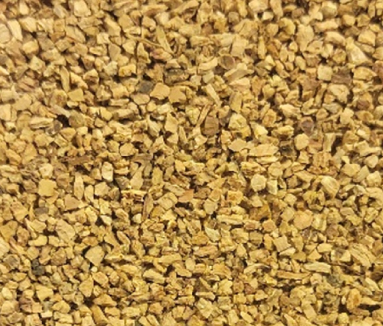
(0.5-1mm)
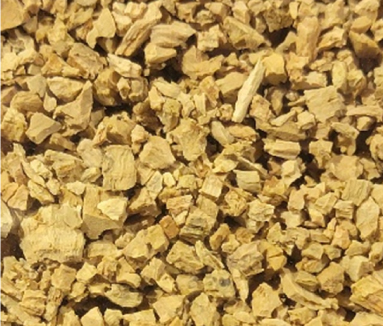
(0.5-1mm)
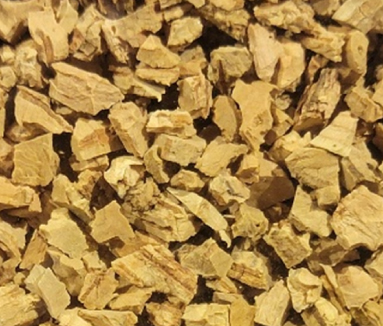
(0.5-1mm)
The granulate is stored and dried until the ideal moisture level is reached based on the desired next step.
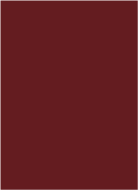
Bonding
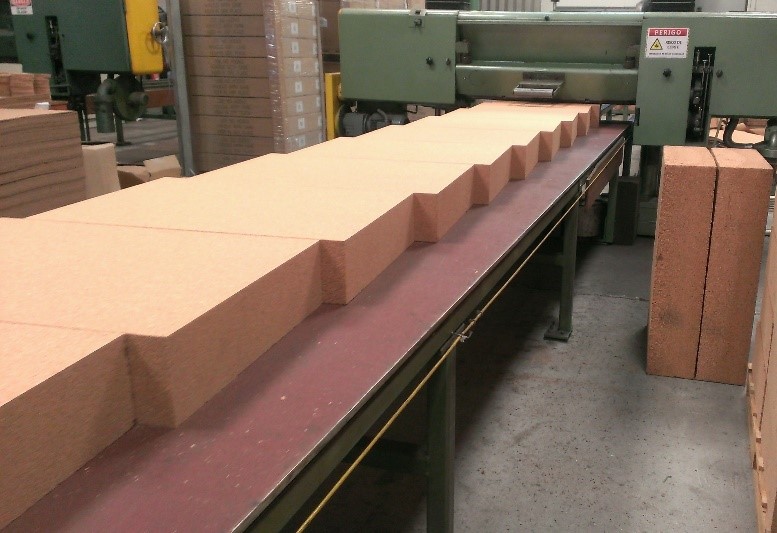
(Natural cork made into blocks)
Cork granules can be bonded together in 2 different ways, either by the use of
steam or with an adhesive.
The steam method, also known as autoclaving, involves heating the granules with steam until they reach between 300-370 oC, at which point the granules undergo expansion and exude a natural resin from the suberin, driving the agglomeration or binding. Once removed there is a noticeable toasted smell for some time (which will eventually dissipate – but it will take some time). The autoclave material is 100% totally natural and considered an ecological agglomerate. Due to the granule expansion, they tend to have a very low density, which in turn gives it high insulating properties, and greater water resilience as there is no external binder.
The other method of creating bonded agglomerated cork is to mix the granules with an adhesive. Typically, the percentage of binder is the range of 2% by volume. The mixture is placed in a heated mold and compressed under pressure. Once the press is released, the material is effectively cured (though it would need to cool). By using natural cork granules (that are un-altered – ie: not going through the autoclave expansion), the material tends to have a higher density. The adhesive bonded material tends to be cleaner (aesthetically and physically), and used more for decorative, interior and high-touch applications.
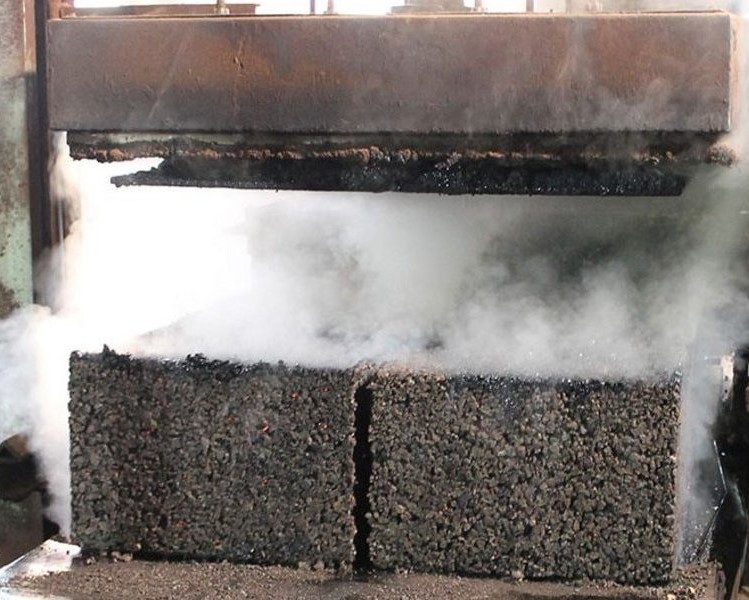
(Bonding granules through ‘autoclaving’)
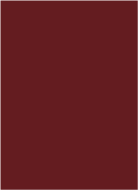
Shaping
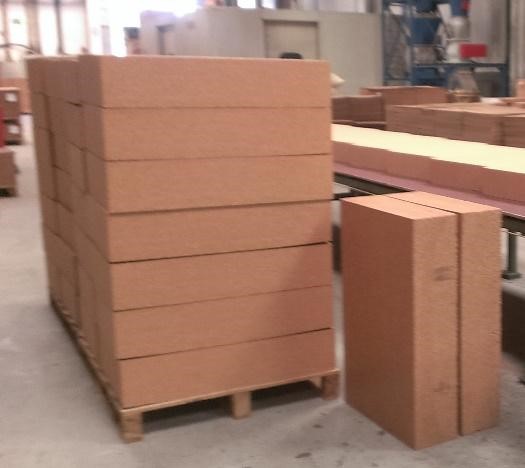
(Shape of a block)
Cork can be molded, from granules, in 3 main ways:
- By being pressed into blocks
- Being pressed into cylinders
- Being pressed into a custom-shaped mold
The most common method of molding cork is to compress the granules into blocks. This involves either agglomeration where adhesive is applied to the granules prior to compression, or having the granules undergo an autoclaving process where steam is applied which internally causes a natural bonding between the cork pieces. The standard production size block for the agglomerated cork is typically around 2’ x 3’ (600mm x 900mm), with a thickness of between 6-8” (150-200mm).
The autoclaved material (also called ‘black’ cork, due to the color the steaming process has on the cork) is made in more varied sizes depending on what will be made. Once the blocks are cured (almost immediately for agglomerated, and a couple hours for autoclaved), they can then be processed: cut into sheets/slabs, combining multiple blocks together for a larger sized starting point, or it can just be used ‘as-is’. Most processing applications involve slicing the blocks into sheets, with the thickness selected based on the proposed application or use.
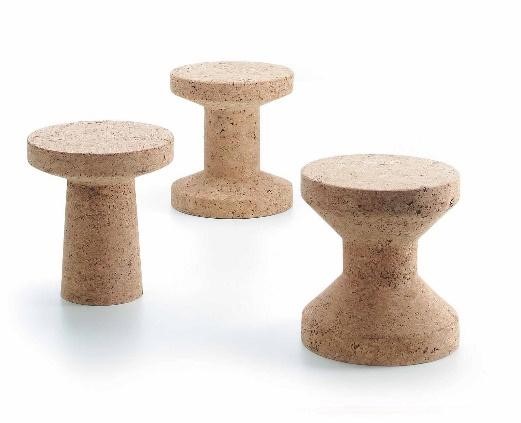
(CNC in block (stool))
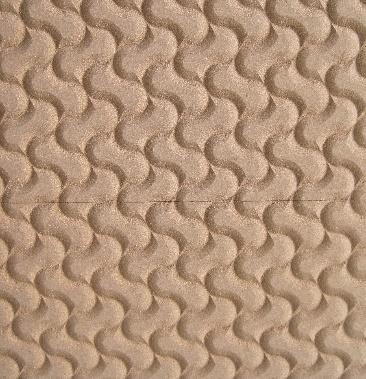
(CNC on flat surface (sedacor 3d))
Though there are no set use specifications for the thickness of the material used, thin layers tend to be used for decorative applications (flooring, walls covering, VCL – Vegan Cork leather), and the thicker ones are used to leverages the materials technical attributes relative to thermal value and acoustics. Additionally, both thin sheets and bigger blocks can further be processed by CNC milling to create 3 dimensional shapes or profiles. A more specialized and unique method of molding the granules is using a cylindrical press mold. This method produces a solid cylinder that can be continually cut to a certain thickness. This process is used for producing decorative veneers that can be produced in long lengths (for panel lamination or VCL creation) and granulated cork rolls (often used for cushioning and sound absorption under flooring).
Made in a similar fashion to the blocks, just with a longer press and cure time, the cork cylinders are peeled in a rotary fashion, seamlessly peeling off the desired thickness that the intended application requires.
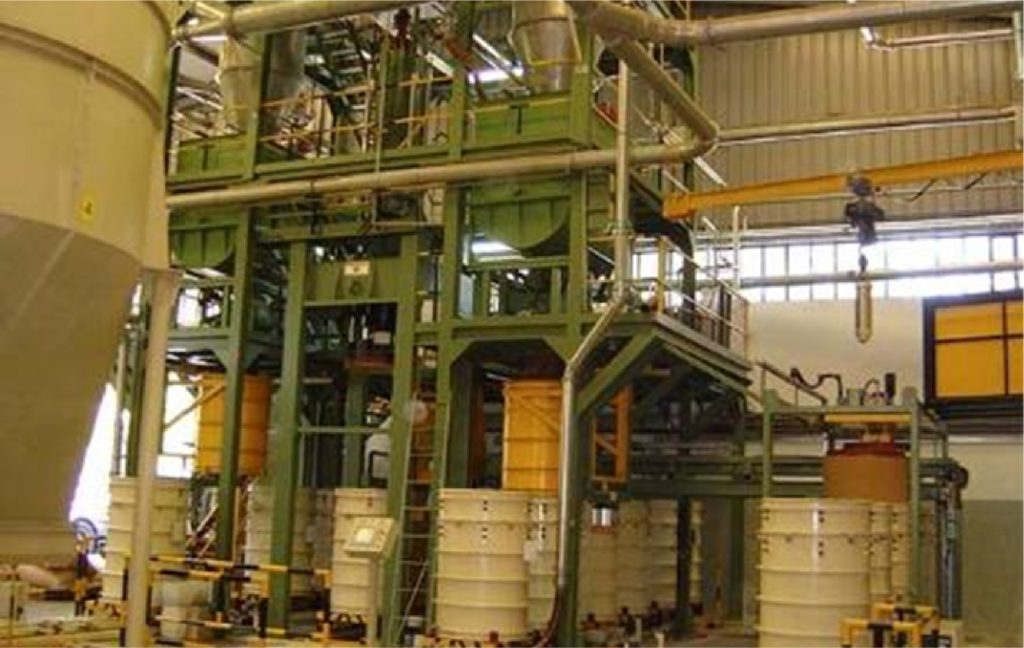
(Cylinder factory)
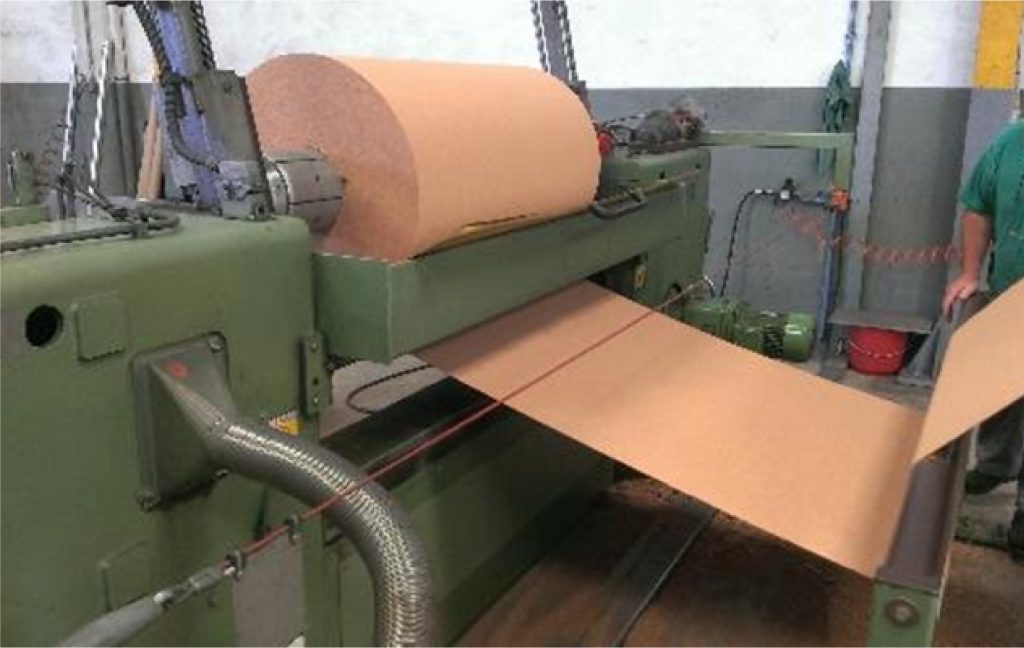
(Compression – agglomerated roll)
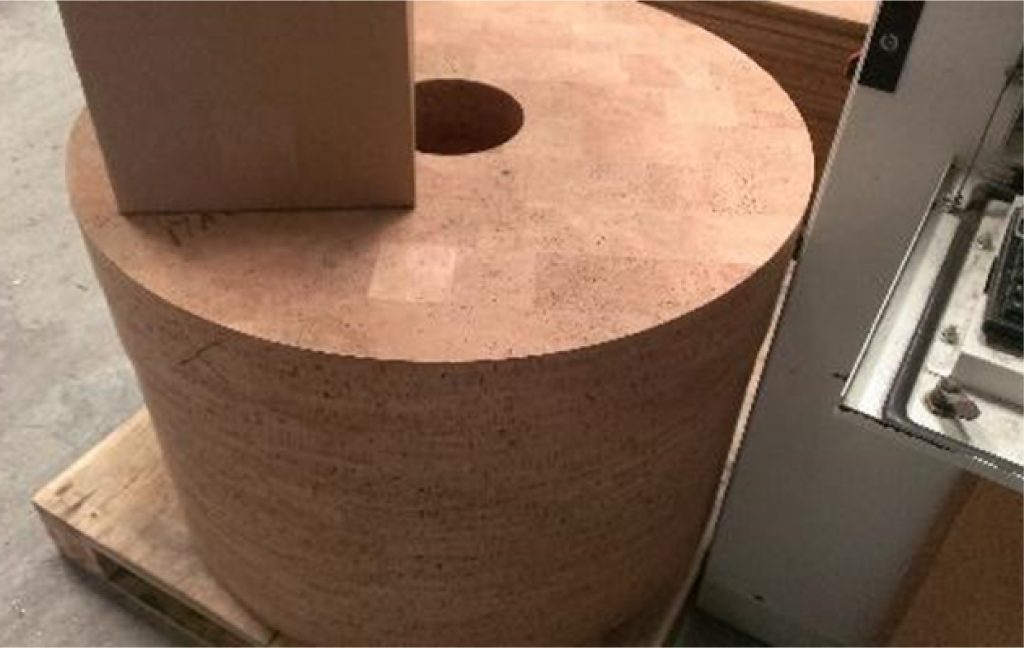
(Compression – decorative role)
The most technologically advanced, and rarest method of shaping cork is via the use of customized molds. The molds, typically made of steel, aluminum, or even silicone, operate in a similar way to the other heated molds, the main difference being that you get exactly the shape you want, and it is just one production process, rather than incorporating different independent procedures that need to be done together to create the final product. Flat sided 3-dimensinal products tend to be the easiest to make, while products with shaped edges on all sides are much more difficult to make due to the specialized manufacturing equipment needed.

(Shoe mold (simply amazing or other))
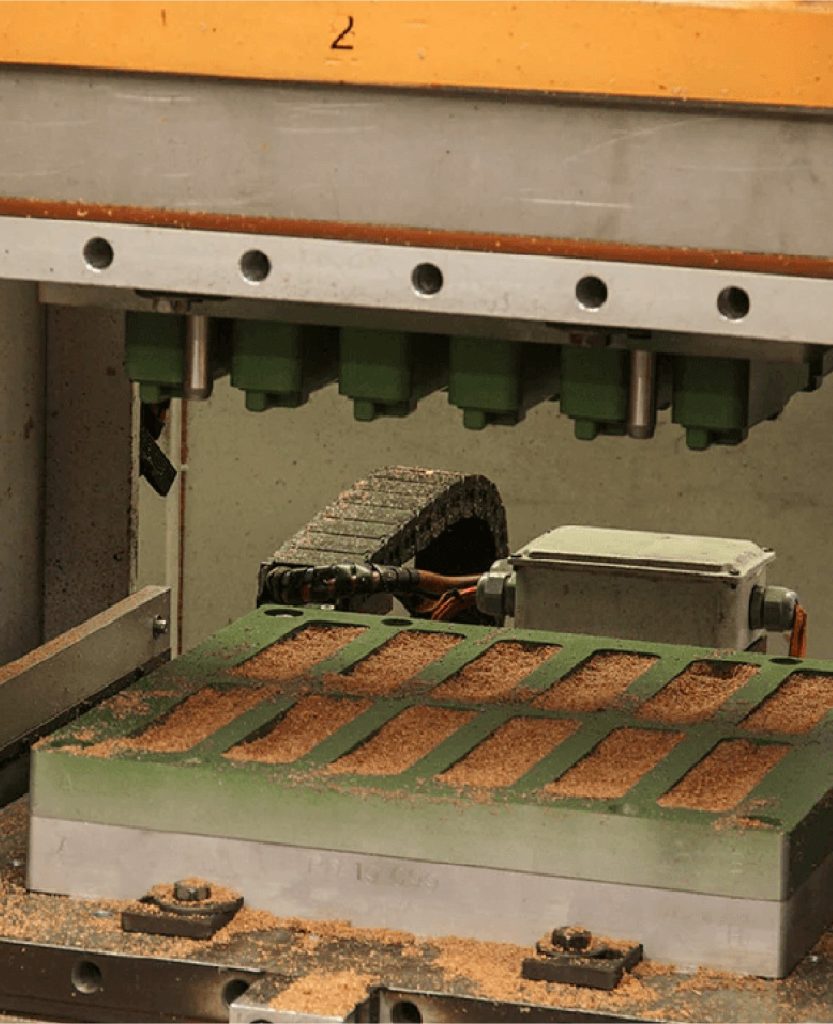
(Small ‘accessory’ mold)
The most technologically advanced, and rarest method of shaping cork is via the use of customized molds. The molds, typically made of steel, aluminum, or even silicone, operate in a similar way to the other heated molds, the main difference being that you get exactly the shape you want, and it is just one production process, rather than incorporating different independent procedures that need to be done together to create the final product. Flat sided 3-dimensinal products tend to be the easiest to make, while products with shaped edges on all sides are much more difficult to make due to the specialized manufacturing equipment needed.
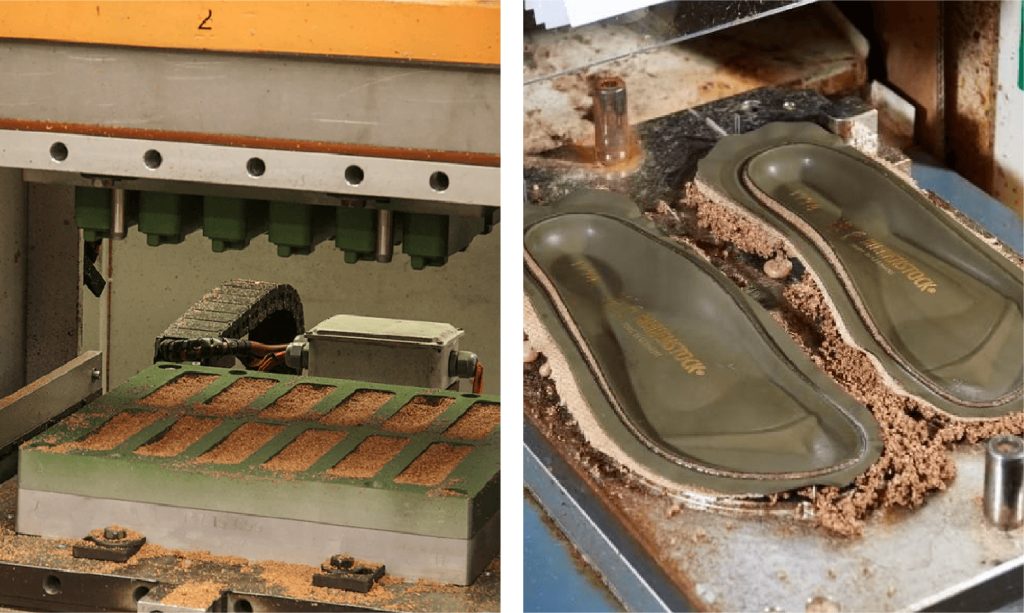
(Granule pigmentation)
(Shoe mold (simply amazing or other))
Cork is probably one of the most flexible materials as it relates to production and making things from it. Being that it is made of small bits (granules) that effectively get added together and get added just to the size it needs to be, there is extremely little waste that ever needs to be created. And the related beauty to that is that any waste created will be used in the creation of other products. It is a full-cycle raw material.
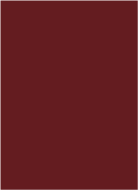
Coloring
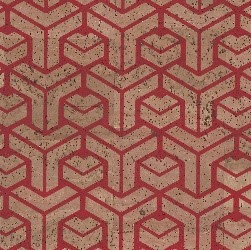
(Printing)
Coloring cork can be done in several different ways: using autoclaved material (ie: ‘black’ cork), staining/painting, pigmenting the granules, or printing directly on the cork.
The process of staining or painting cork is no different than staining or painting another species of wood. The result will be similar – you only get a lot more ‘design’ choices when using cork (due to all the different patterns that the cork raw material can be made into).
Color-infusion is a new technique using pigmented material. The value of through-color cork really manifests itself when it is used in the 3-dimensional molding fabrication technique. When done properly, the entire exterior perimeter of the pigmented product will have a consistent color intensity.
And, if chipped or cut in half, that color would be in the inside as well.
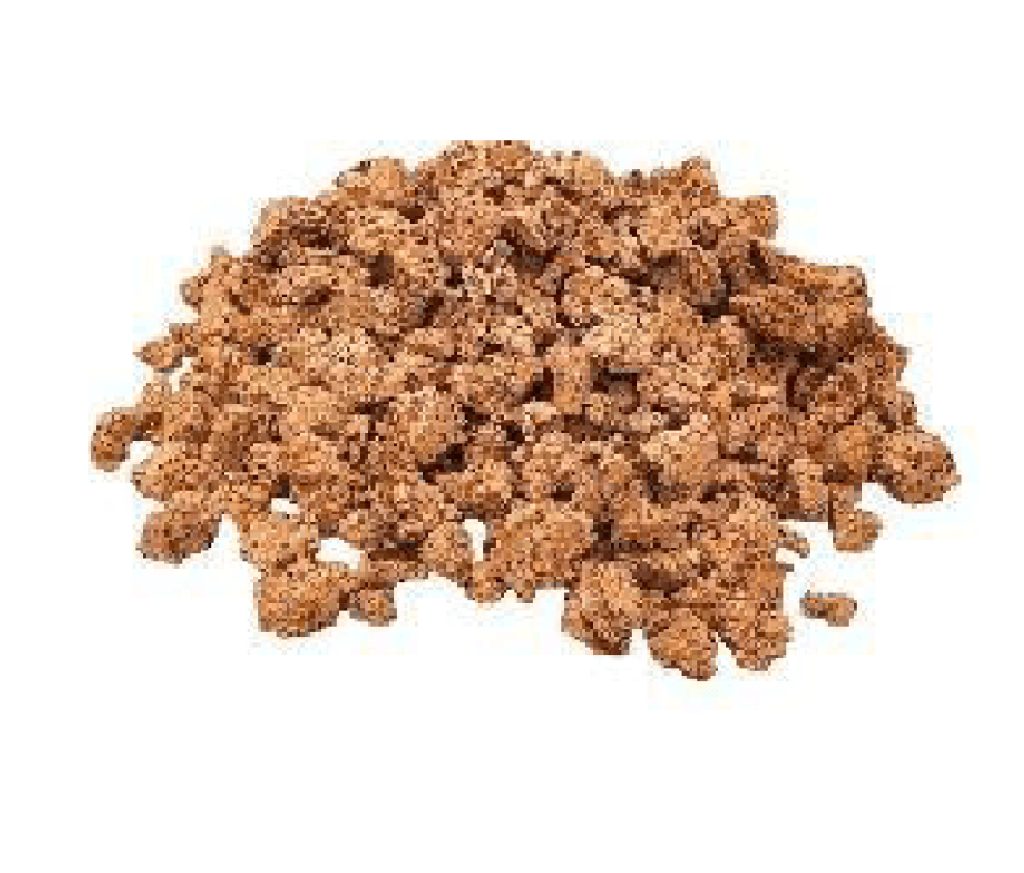
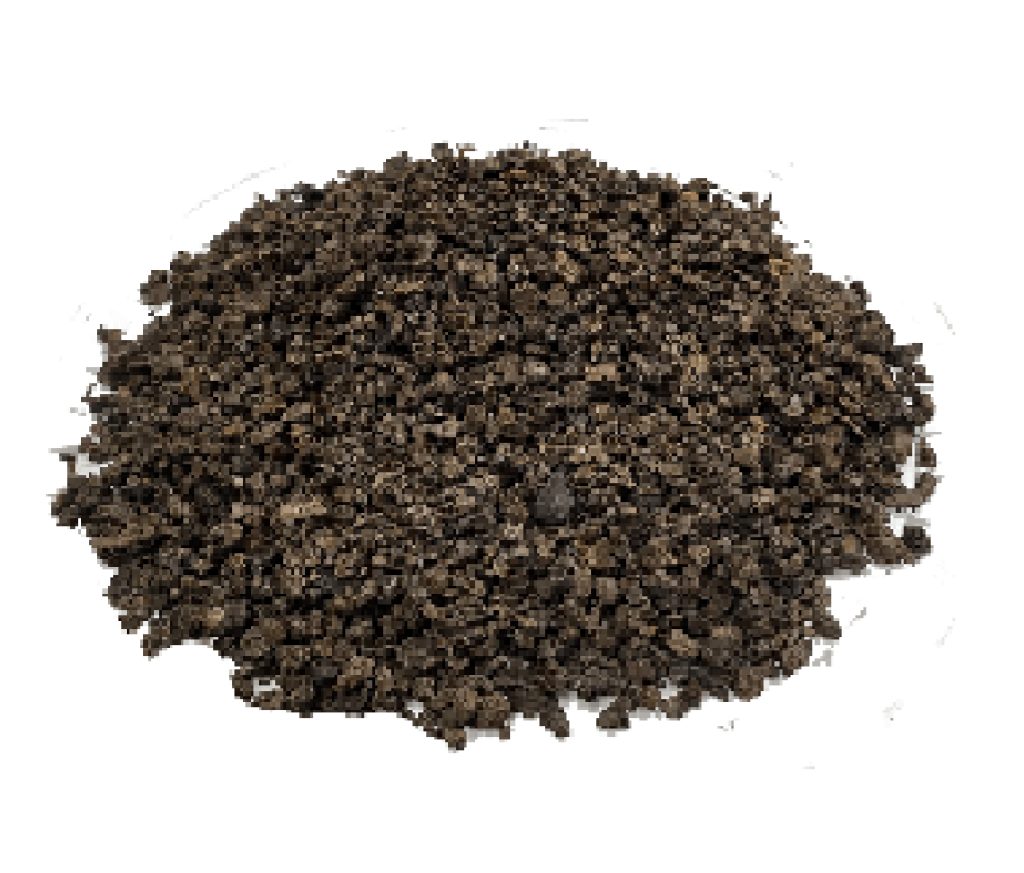
(Natural and autoclaved)
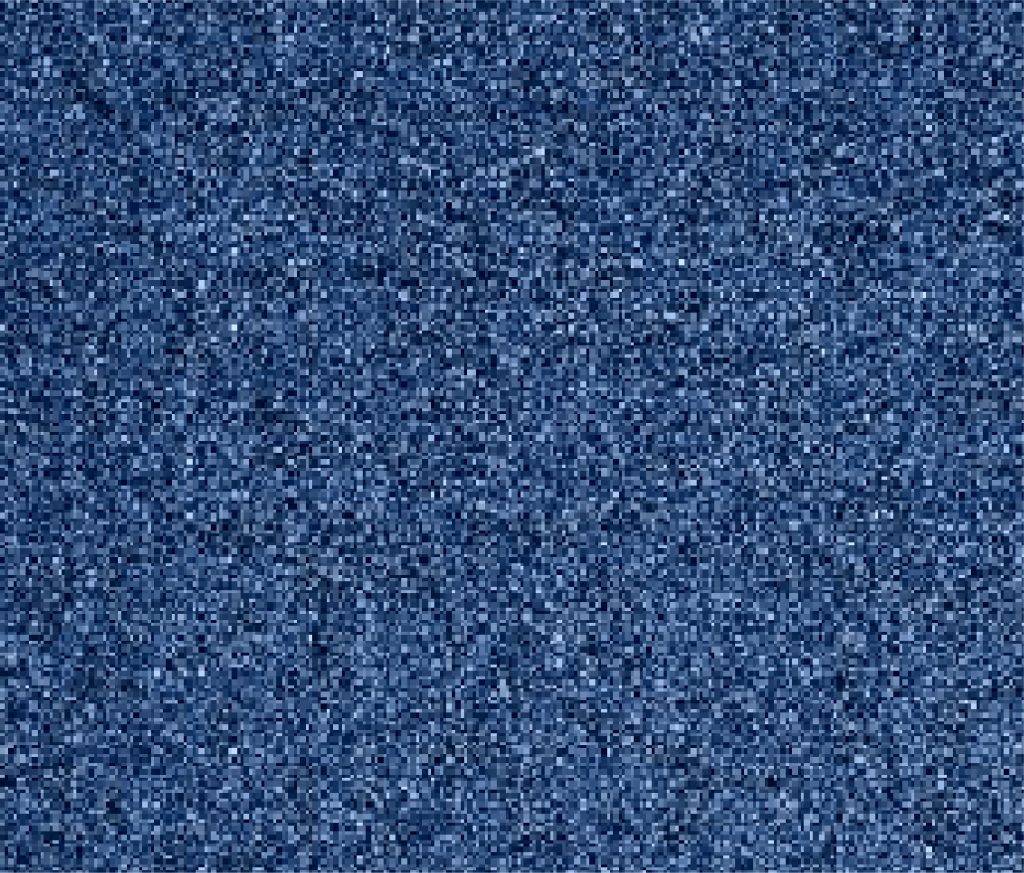
(Granule pigmentation)
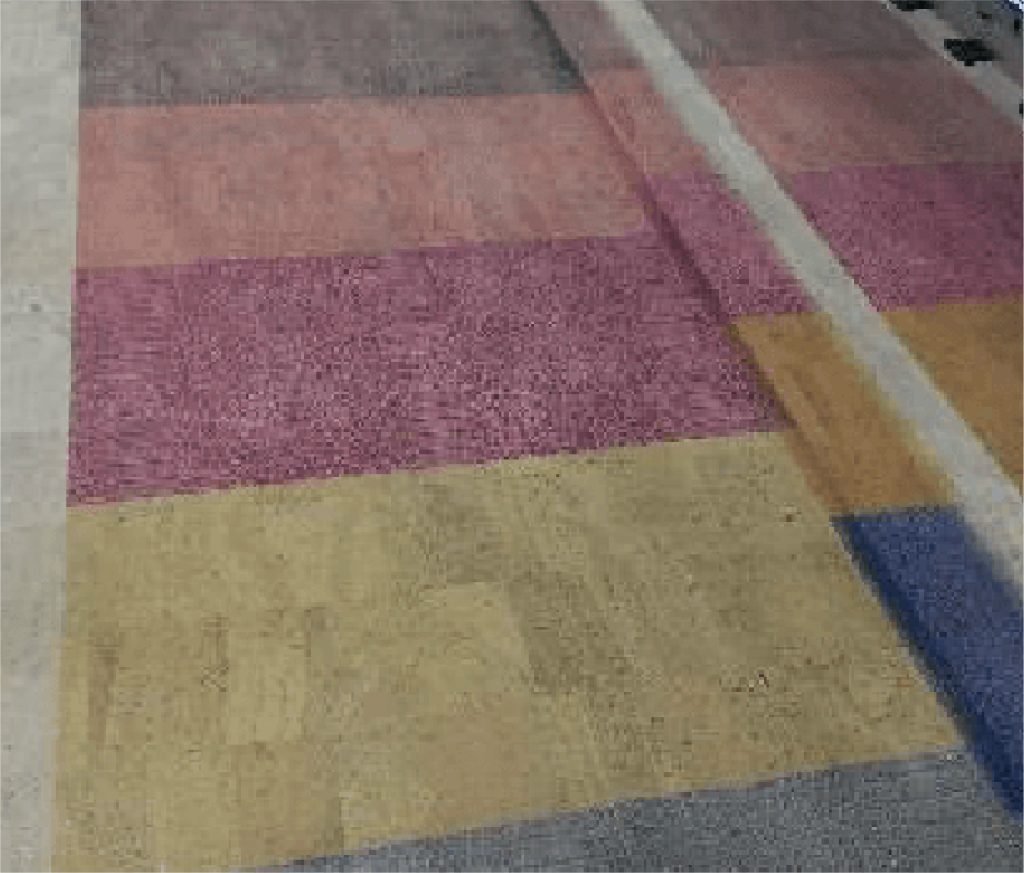
(Staining/painting)
(Natural and autoclaved)
(Granule pigmentation)
(Staining/painting)
Cork can also be printed upon, though this is typically reserved for the handbag, personal accessory, and the sporting goods market segments. VGL can easily be run through a laser printing process, so your creativity or created design can easily be transformed onto the cork surface.