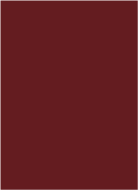
Shaping
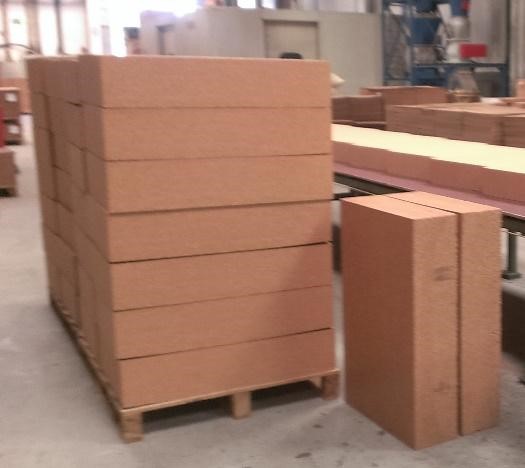
(Shape of a block)
Cork can be molded, from granules, in 3 main ways:
- By being pressed into blocks
- Being pressed into cylinders
- Being pressed into a custom-shaped mold
The most common method of molding cork is to compress the granules into blocks. This involves either agglomeration where adhesive is applied to the granules prior to compression, or having the granules undergo an autoclaving process where steam is applied which internally causes a natural bonding between the cork pieces. The standard production size block for the agglomerated cork is typically around 2’ x 3’ (600mm x 900mm), with a thickness of between 6-8” (150-200mm).
The autoclaved material (also called ‘black’ cork, due to the color the steaming process has on the cork) is made in more varied sizes depending on what will be made. Once the blocks are cured (almost immediately for agglomerated, and a couple hours for autoclaved), they can then be processed: cut into sheets/slabs, combining multiple blocks together for a larger sized starting point, or it can just be used ‘as-is’. Most processing applications involve slicing the blocks into sheets, with the thickness selected based on the proposed application or use.
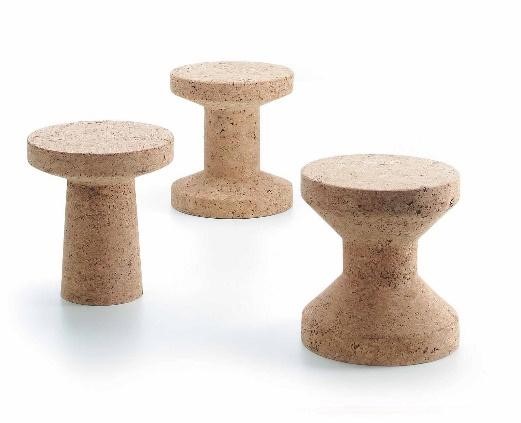
(CNC in block (stool))
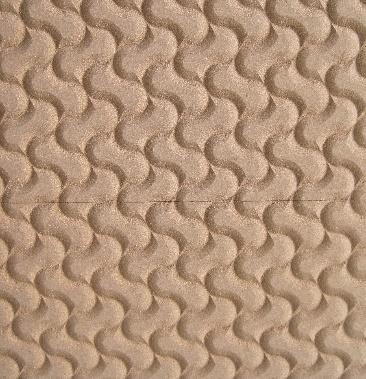
(CNC on flat surface (sedacor 3d))
Though there are no set use specifications for the thickness of the material used, thin layers tend to be used for decorative applications (flooring, walls covering, VCL – Vegan Cork leather), and the thicker ones are used to leverages the materials technical attributes relative to thermal value and acoustics. Additionally, both thin sheets and bigger blocks can further be processed by CNC milling to create 3 dimensional shapes or profiles. A more specialized and unique method of molding the granules is using a cylindrical press mold. This method produces a solid cylinder that can be continually cut to a certain thickness. This process is used for producing decorative veneers that can be produced in long lengths (for panel lamination or VCL creation) and granulated cork rolls (often used for cushioning and sound absorption under flooring).
Made in a similar fashion to the blocks, just with a longer press and cure time, the cork cylinders are peeled in a rotary fashion, seamlessly peeling off the desired thickness that the intended application requires.
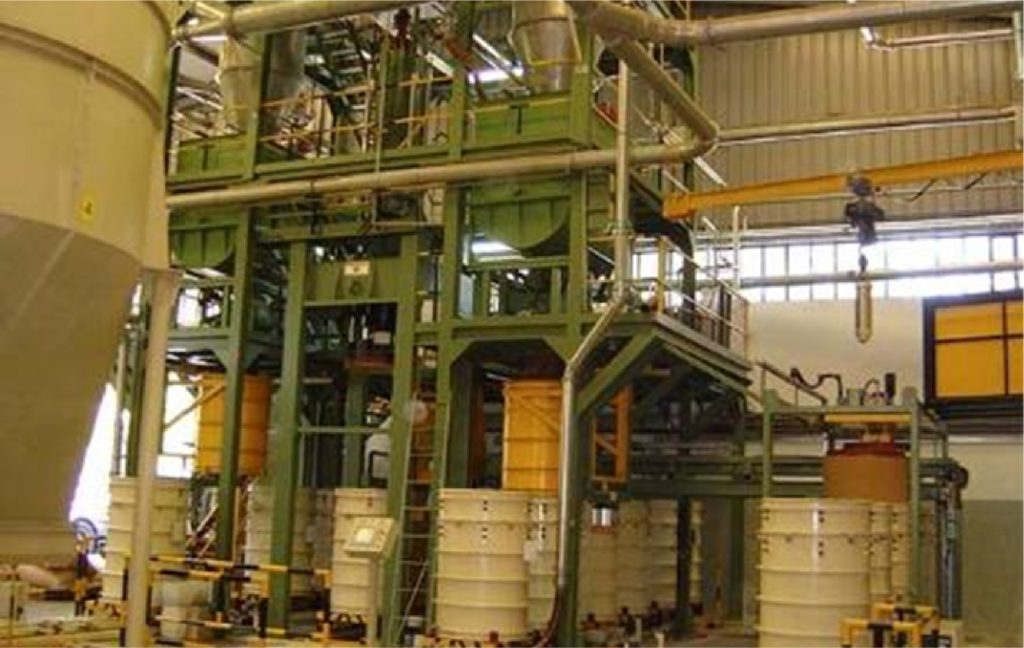
(Cylinder factory)
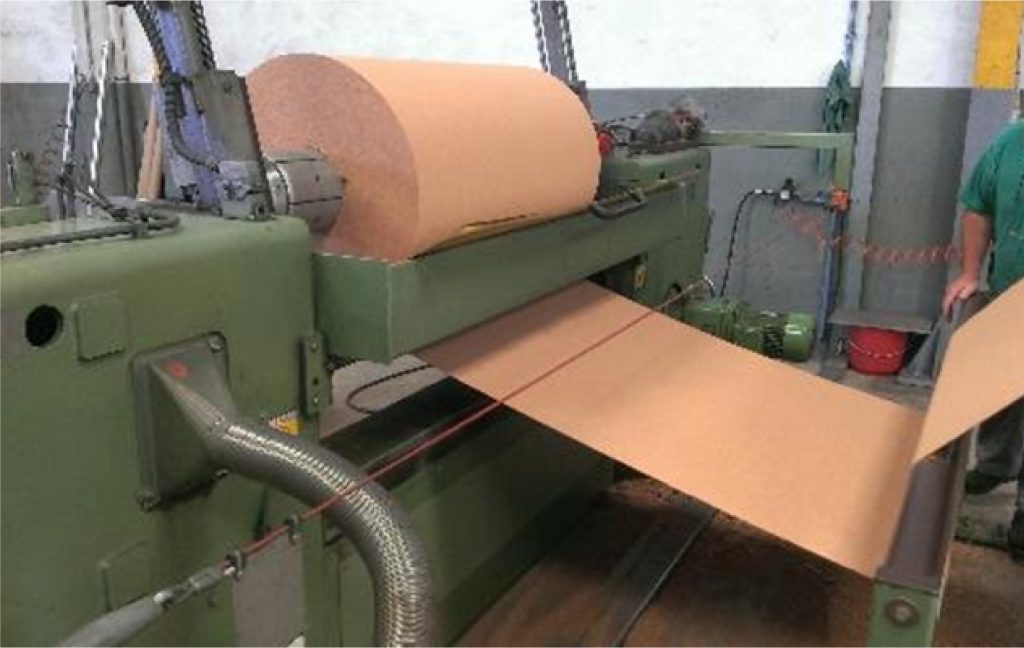
(Compression – agglomerated roll)
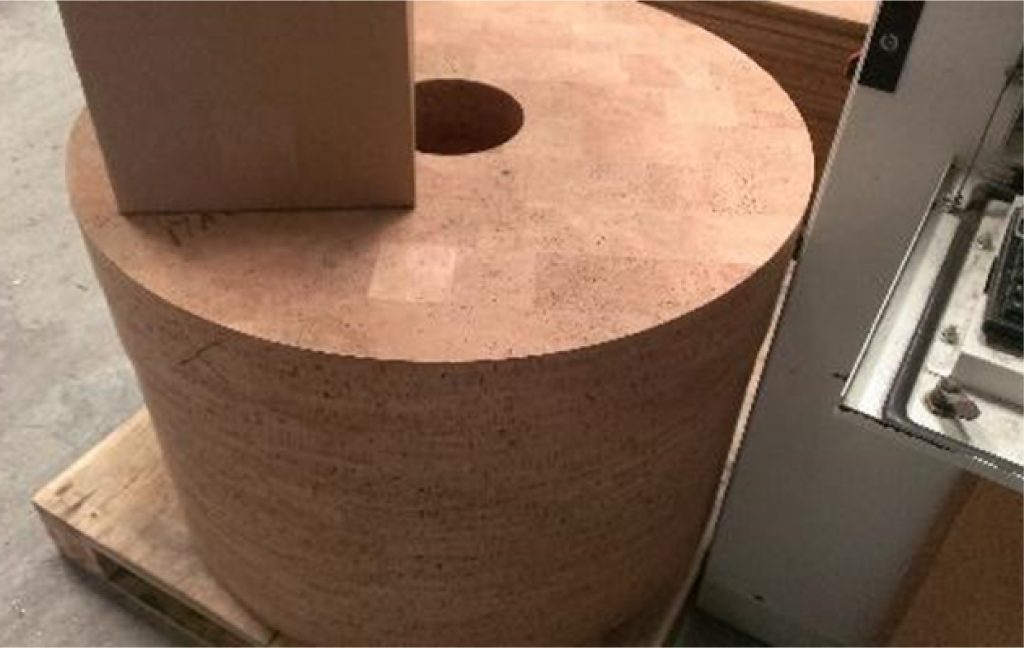
(Compression – decorative role)
The most technologically advanced, and rarest method of shaping cork is via the use of customized molds. The molds, typically made of steel, aluminum, or even silicone, operate in a similar way to the other heated molds, the main difference being that you get exactly the shape you want, and it is just one production process, rather than incorporating different independent procedures that need to be done together to create the final product. Flat sided 3-dimensinal products tend to be the easiest to make, while products with shaped edges on all sides are much more difficult to make due to the specialized manufacturing equipment needed.

(Shoe mold (simply amazing or other))
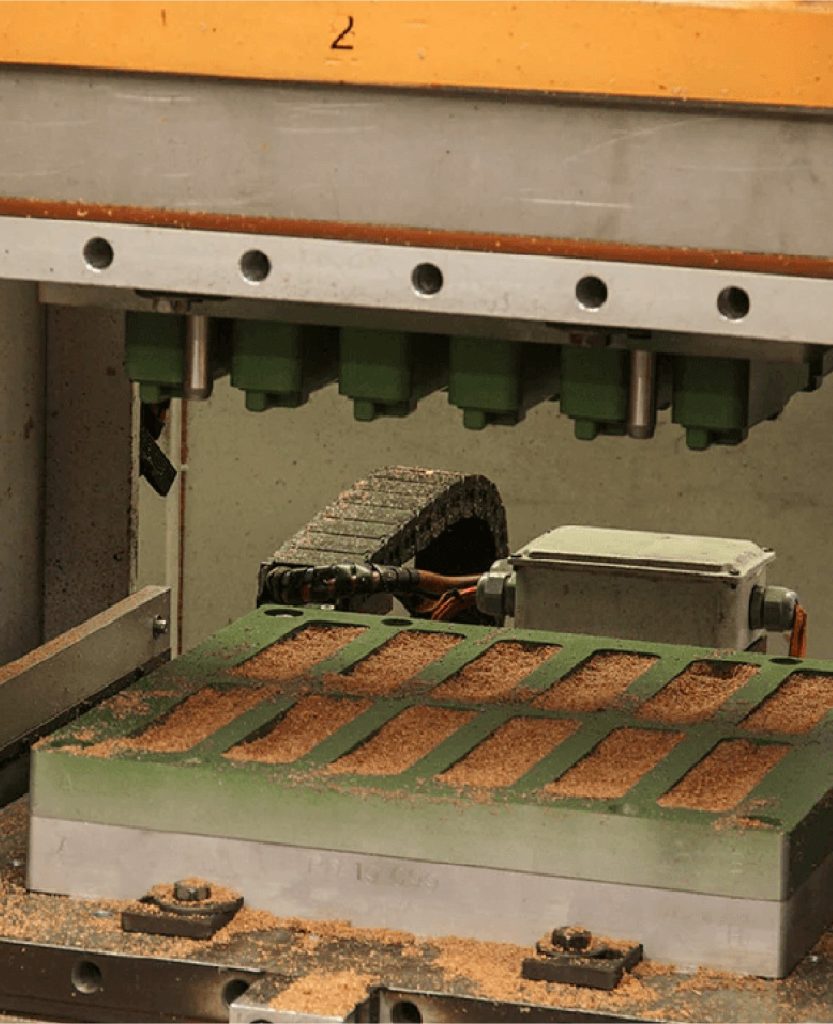
(Small ‘accessory’ mold)
The most technologically advanced, and rarest method of shaping cork is via the use of customized molds. The molds, typically made of steel, aluminum, or even silicone, operate in a similar way to the other heated molds, the main difference being that you get exactly the shape you want, and it is just one production process, rather than incorporating different independent procedures that need to be done together to create the final product. Flat sided 3-dimensinal products tend to be the easiest to make, while products with shaped edges on all sides are much more difficult to make due to the specialized manufacturing equipment needed.
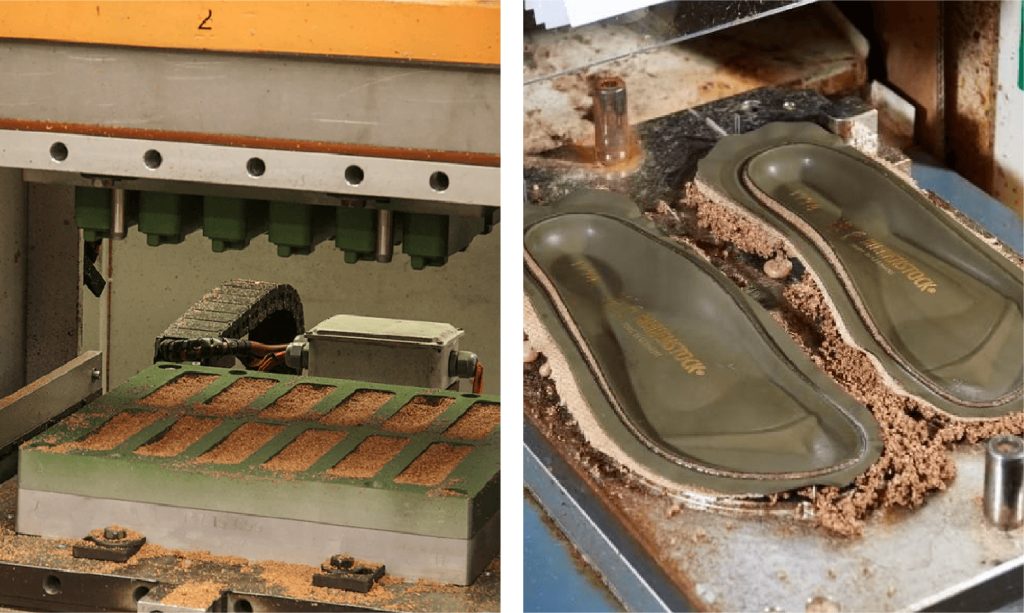
(Granule pigmentation)
(Shoe mold (simply amazing or other))
Cork is probably one of the most flexible materials as it relates to production and making things from it. Being that it is made of small bits (granules) that effectively get added together and get added just to the size it needs to be, there is extremely little waste that ever needs to be created. And the related beauty to that is that any waste created will be used in the creation of other products. It is a full-cycle raw material.